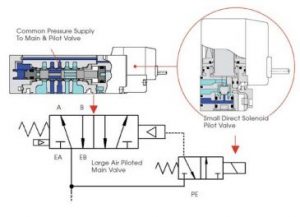
How SMC solenoid valves are designed to reduce energy consumption
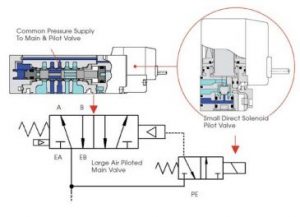
Flow amplification helps solenoid valves save power.
Advanced Motion & Controls Ltd. supplies a variety of products by SMC Pneumatics, including many models of solenoid valves. One advantage of trusting SMC for these directional control valves is their low power consumption. The manufacturer uses modern valve design to lower the use of energy.
Flow amplification is one of the key ways SMC produces products that do not waste power needlessly.
Smaller size for energy savings
Decades ago, pneumatic valves were manufactured with large, direct solenoids and bulky steel construction. These solenoid valves often consumed six watts of power and lasted for ten million cycles. Today, SMC makes ones that users can operate on power of only one-tenth of a watt, but that last for more than 200 million cycles. This is possible through innovative valve design.
A common technique for reducing energy consumption in pneumatic valves is flow amplification. In this concept, a very small, three-port, two-position, direct-solenoid valve operates a much larger, air-operated valve, and the smaller solenoid results in low energy use. This development has led in recent years to direct-solenoid valves that are smaller in size and consume less power.
As valve design has changed, so have the materials used, from zinc die cast to anodized aluminum and engineering plastics. Today, Advanced Motion & Controls Ltd. offers SMC valves with streamlined shapes and smaller masses, with internal passages, spools, sleeves, and poppets designed for more flow capacity.
SMC offers the following practical tips for getting further cost and energy savings from its solenoid valves:
- Apply energy-efficient valves whenever possible. Replacing older, less efficient ones can be part of a major overhaul or on a replace-as-needed basis.
- Shop for energy-efficient machines. Ask builders how products were designed with energy savings in mind.
- Build energy-efficient machines. Use power amplification and always consider mechanical advantages.
- Use the correct amount of air pressure. Never use more than necessary.
- Avoid using “air blow” applications. If air blow is required, use efficient nozzle designs.
- Use the “off” switch. Turn off machines when not in use.
For more information, contact Advanced Motion & Controls.